ダイカスト金型
YAMADAは、アルミダイカスト金型を中心に金型の設計、製作を行っています。
-
ダイカスト金型
金型製作工程
設計工程では、CAE解析を用いて製品仕様検討や方案設計をスタートし、3D設計から加工プログラムまでを一気通貫で行っています。
製作工程では、マシニングによる直彫り加工や無人加工を追求し、鋳造トライ後の製品測定では、高い1トライ合格率を実現し、高品質かつ低廉な金型を世界へ提供しています。
また、自社鋳造工場で、量産時の鋳造条件や品質の見極めまでを行えることが強みとなっています。
-
①鋳造CAE解析 -
②設計 -
③加工プログラム
-
④加工 -
⑤組付け -
⑥トライ
-
⑦検査
鋳造CAE解析
信頼性の高い鋳造CAE解析で金型方案の早期熟成による立上げロスを削減します。
鋳造量産時の品質結果をフィードバックし、高精度化を実現しています。
-
溶湯充填率 -
溶湯温度
-
ガス量 -
引け巣
設計
独自に標準化された3D金型設計システムとともに、自社鋳造で得たノウハウ/ニーズを盛り込み
高品質な鋳造品を生み出す金型モデルの設計をスピーディーかつタイムリーに行っています。
-
独自標準化テンプレートによる
高精度3Dモデル設計 -
3D金型 アセンブリ設計
加工プログラム
独自技術である熱処理前加工レス化による熱処理後に加工を集約させて高効率加工を行い、
工程をシンプル化することでロングラン加工による無人稼働拡大とリードタイム削減を実現しています。
-
加工プログラム作成 -
2.5軸加工プログラム作成
-
加工切削アニメーション
加工
縦型M/C(マシンニングセンタ)を揃え、直彫り加工を主体として1250トンクラスのダイカスト金型製作に対応し、各加工機で600時間/月以上の稼働を実現しています。
また、大型の横型M/Cを活用しモールドベースを加工しています。
-
縦型マシニングセンタ -
直彫り加工 -
加工完成品
-
横型マシニングセンタ -
モールドベース加工
組付け
金型手仕上げ~組付け
擦り合わせ作業ゼロ化に向け、経験、カン、コツによる作業を3Dモデルへフィードバックし、組付け作業の簡素化及び高効率化を図っています。
最終型合わせ精度向上へ向け、ダイスポ型合わせを実施します。
また、金型の応力測定を行い、適正メンテナンスのタイミング見極めに取り組んでいます。
-
組付け -
ダイスポッティングプレス -
応力測定
トライ
長年培った鋳造技術と品質評価指標による定量的な評価を実施します。
品質及び量産性を踏まえた最適鋳造条件を提案します。
-
溶湯品質評価 -
金型表面温度測定(サーモビューワー) -
内部品質評価(X線CT測定)
検査
加工後金型部品~金型組付け後の3D測定/照合を実施しトライ前の金型保証を行う事で製品寸法の高い一発合格率を実現しています。
トライ後アルミ製品の全寸法測定と3D照合評価を行い、形状保証まで行っています。
製品のカメラ測定(STL)データから3Dモデル化のリバースエンジニアリング業務も行っています。
-
カメラ式三次元測定器 -
金型3Dモデル照合 -
製品3Dモデル照合
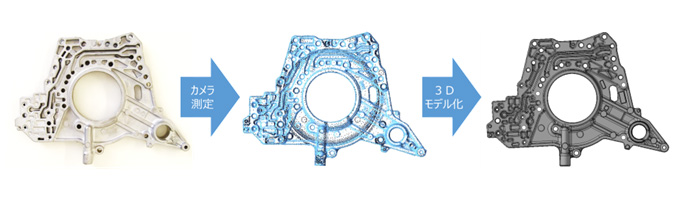
-
製品 -
測定データ
STL -
3Dモデル
IGES,STEP
保有設備
縦型マシニングセンタ | 5台 | 鋳造解析ソフト | 2ライセンス |
横型マシニングセンタ | 1台 | 3D-CAD | 6ライセンス |
型彫り放電加工機 | 2台 | 2D-CAD | 4ライセンス |
ワイヤー放電加工機 | 2台 | 3D-CAM | 5ライセンス |
グラファイト加工機 | 1台 | 対応データ | CATPart Parasolid ACIS STEP IGES |
平面研削盤 | 2台 | ||
ダイスポッティングプレス | 1台 | ||
ショットブラスト | 1台 | ||
三次元測定機 | 3台 | ||
カメラ式三次元測定器 | 2台 |