生産領域
独創的な技術力を活かし、生産システムを内製化
YAMADAのもの造りは、製品のみにとどまりません。独創的な技術力は、あらゆる工程において発揮されます。全生産設備の70%以上を自社で製作しているほか、鋳造で使用する金型の多くも内製しています。生産設備から金型までを自社で開発・設計・製造し、国内外の各製造拠点に最適なラインを構築することで、高品質な製品を効率よく生産できる体制を整えています。こうした生産システムの内製化が、YAMADA製品の高い信頼性につながっています。
生産技術・開発
設備設計技術を活用し、ハードからソフトまで自社内で開発を行っています。小型冶具から大型トランスファーマシンまで、自社製作の割合は全生産設備の70%以上にもおよび、アルミダイカスト鋳造、焼結などの各工程で使われる金型の多くも製作しています。これらの生産設備・金型は全世界に向けて販売も行っております。
さらに、次世代製品の生産技術開発を行い、その技術を活かした生産設備や金型を幅広く内製するシステムは、製品の信頼性・設備効率および生産性の向上に繋がっています。
設備製作体制
全世界に向けた最適なライン構想を提案し、信頼性の高い製品を製造するために、高精度・高品質の設計を行い、お客様に満足していただける製品を製造する設備製作を行っています。
また、自社の開発用として開発部門で使用される耐久試験機や性能試験機についても設備製作を行い、製品の信頼性確認体制に寄与しています。
CADによる設備設計 内製設備製作 多関節ロボットによるバリ取り加工 チェーンケース自動加工ライン ステアリングコラム組立ライン 内製設備
(性能試験機)
金型開発
アルミダイカスト金型を主に金型製作を行っています。設計については流動解析・凝固解析等を行い、その結果を金型設計に反映させています。製作についてはCAMにて加工でデータを作成し可能な限りの無人加工で、高品質かつ低廉な金型製作を実現し、全世界へ提供しています。
流動解析
(金型の湯流れ解析)金型設計
(3D CADによる金型設計)製品、金型検査
(カメラ、レーザー三次元
測定器による測定)CNC治具ボーラー
(金型直彫り加工用
高速マシンニングセンタ)横型マシニングセンタ
(主型、大物金型加工用)内製金型
(CVT部品から
大型オイルポンプまで製作)
生産ライン
YAMADAの主要機能部品は塑形材成形から加工・組立までを一貫生産し、自働化(自ら働く)にて高効率・高品質を実現しています。
鋳造領域
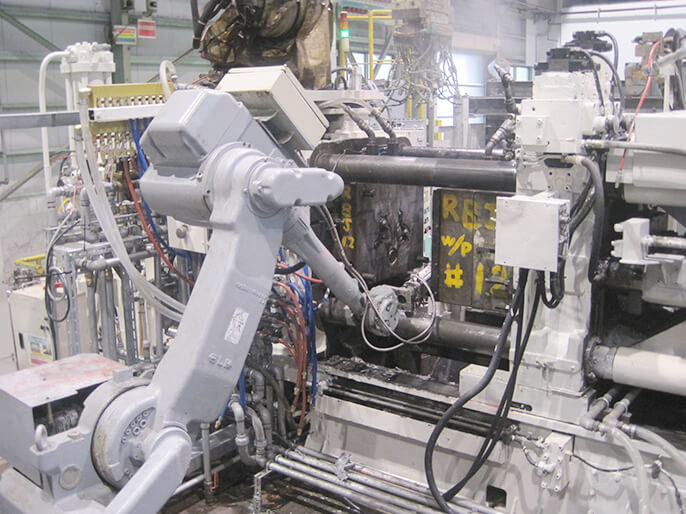
自社で設計製作された精密金型を用い、複雑な形状で難易度の高い肉薄アルミ部品を大型品から小型品まで幅広く生産しています。金型仕様は量産より得られたノウハウや流動解析及び凝固解析結果をフィードバックすることで、一般的なアルミニウム材はもとより耐摩耗性を有した流動値の低いアルミニウム材においても高品質にて安定生産を実現しております。
焼結領域(成形・焼結・再圧・加工)
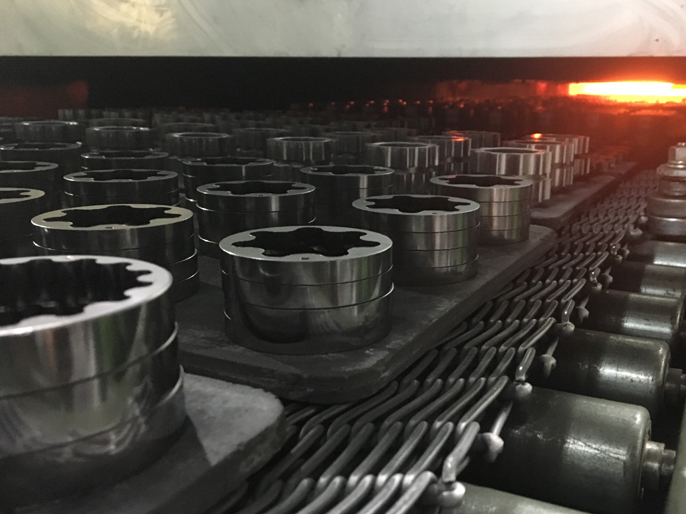
素材の鉄粉を精度の高い金型を用いて、プレスによって成形後、高温の焼結炉にて焼成し、お客様の規格通りの形状に再圧工程で矯正した後、CNC旋盤や研削盤の加工工程で更に高い精度に仕上げています。伊勢崎焼結工場は焼結部品を自社開発し、塑加工一貫体制にて生産をしております。
加工領域
切削工程他
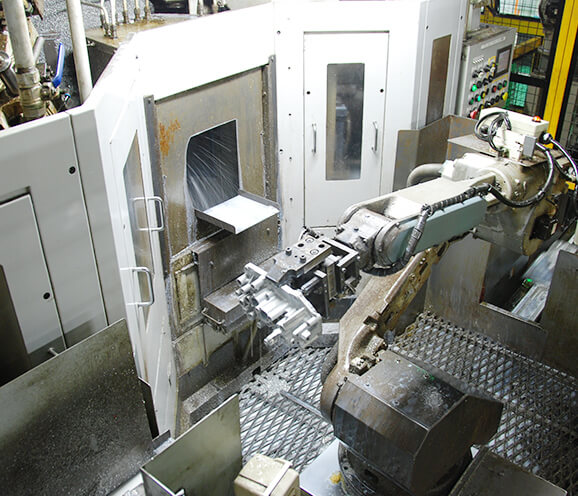
加工領域では高速搬送ローダーやレーン搬送機を用い、素材投入から完成までの一貫した完全自動化ラインを採用。高効率で低コストな安定生産を実現しています。
高精度な切削加工設備はもちろんのこと、多様な工作設備・加工技術を有しており、お客様のあらゆるニーズにお応えしています。
高周波焼入れ
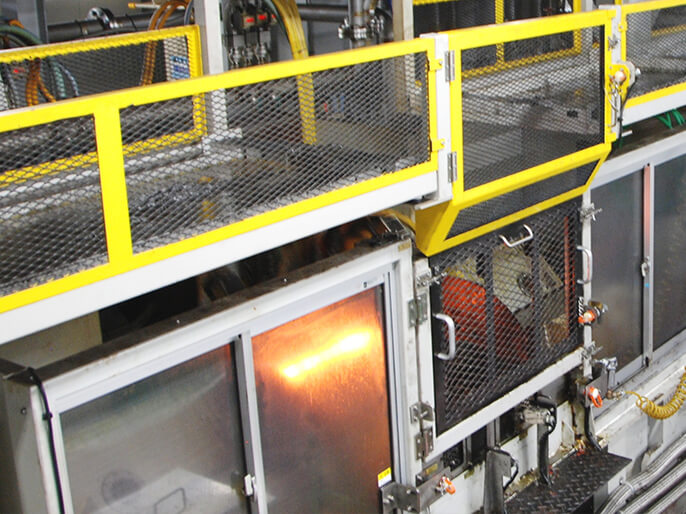
インターミディエイトシャフト(ハーフシャフト)生産ラインでは高周波によるワンショット焼入れ法を用いて、曲がりが少なく均等な表面温度を確保することで高品質を維持すると共に、加工工程内へインライン化することで高効率・安定生産をしております。
また、ステアリングコラム用シャフトではハンドルロック部のキー穴に高周波焼入れを施し、キー穴の表面硬度UPを図り、耐摩耗性を向上させています。
鍛造
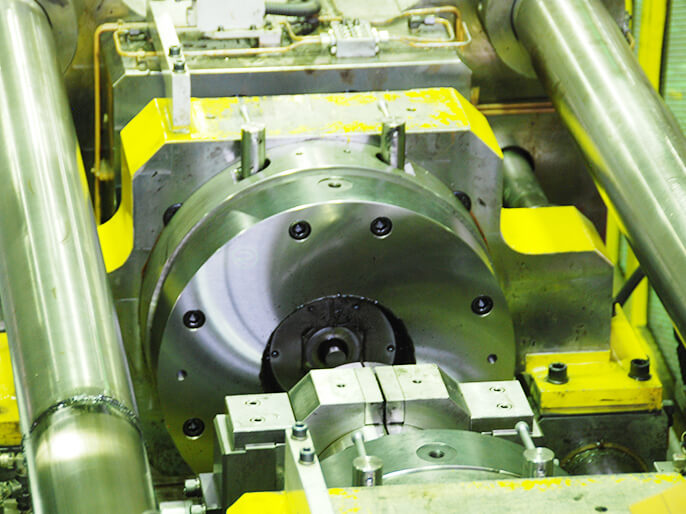
金属素材を室温で金型を用いて圧縮成型する冷間鍛造方式を採用しています。 この加工法の優れている点は、短いタクトで最終形状まで作ることができるところです。これにより、表面仕上げおよび高精度な部品が得られるので、完成品に近い形状に加工でき、切削などの後工程が最少限となり、加工時間を短縮することが可能です。
溶接
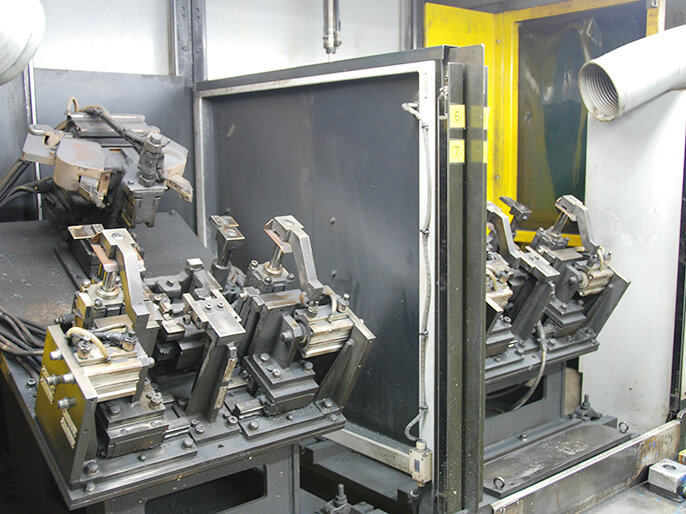
ブラケット溶接ではプレス工程で生産されたステアリングコラム用部品を組み合わせて、複数のポイントをロボットにより溶接することで、安定した再現性と高効率化を実現した溶接ラインです。
パイプ溶接工程ではロボットにより自動で溶接することで出来栄え品質を保証しています。
シャフト溶接は、TIG溶接法※1によるチリ※2の『ゼロ化』を実現し、後始末作業レスを達成。高品質にも大きく貢献しています。人作業や設備もシンプル化し、廃棄物の削減で環境にやさしい生産ラインです。
- ※1:TIG溶接=タングステンイナートガス溶接
電極にタングステン、シールドガスに不活性ガスを吹きつけ、きれいな溶接跡を得る溶接法 - ※2:チリ=溶接時に発生する火花状の溶けた粒状金属(スパッタ)
組立領域
YAMADAでは高効率・低コストにて製品をお客様に提供するために、年間600万台に及ぶ主要製品の組立を自働フリーフローラインと人作業の最適な組み合わせで生産しております。
品質保証においては、工程ごとに品質確認機能が備わっており、高品質で安定的な量産が可能です。
また、高効率・高品質・低コストを達成するとともにクリーン度要求にも応えるために専用クリーンルームを備えるなどライン設計も工夫しています。